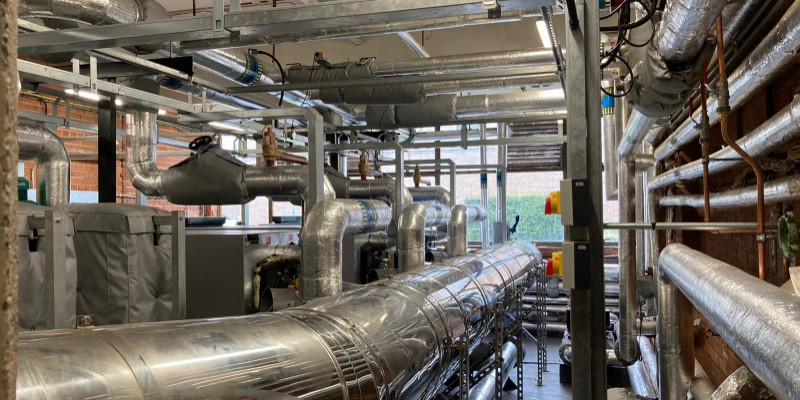
School Boiler Replacement
Challenge
The existing oil-fired school heating system was suffering regular malfunctions due to the age of the existing oil-fired boilers. The costs of individual repairs were escalating and did little to abate the cascade of further heating failures.
Both the domestic hot water and multiple heating zones around the school were served from the central plant room. However, the organic growth of the system over the years had resulted in a disorganized hydronic arrangement that was difficult to control.
The controls installation had no facility to operate the heating zones, cycle boiler usage, or automatically switch off the heating in winter so that only the domestic hot water generators were served.
Only a holistic refurbishment would be effective.
Opportunity
- To replace the old boilers with new plant from a market leading manufacturer.
- To rationalise the hydronic anomalies in the plantroom for reliable, predictable operation.
- To introduce new BMS controls so that all heating zones could be individually operated.
- To engineer in resilience so that the system will operate for years to come.
- To bring the school heating system back into complete working order.
Engineering and Design
The condition of the existing heating in the school was unknown. It was likely that it harboured debris and suffered poor water quality.
Experience suggested that the new boilers could get damaged by dirt in the system.
To protect the new plant, we engineered a system with plate heat exchangers to separate the new plant from the existing heating system.
Plate heat exchangers use metal plates to transfer heat between two fluids without allowing them to mix.
Our Approach
We made a full survey and measure of the plant room and drew up the results in CAD. We assessed the condition of the equipment in the plantroom and helped to decide what needed to be replaced. We produced ‘as existing’ ‘alterations’ and ‘as proposed’ plantroom layouts so that our client could fully understand what the works entailed.
We drew up existing and new plantroom heating schematics to understand how to optimise the heating operation.
We investigated a variety of boiler selections to ensure that the right combination of heating plant was installed to fit the plantroom and cover the heating loads.
We simplified the pipework in the plantroom to improve the hydronic arrangement and bring the system under reliable control.
We worked in partnership with the controls specialist to ensure that all plant worked in sequence under the dictates of the new BMS.
We produced a complete plantroom refurbishment package including drawings, equipment schedules, control specification and designers risk assessment.
We were on hand during installation to answer queries.